econfly
Member
This question came up in an ESC product review I wrote. Say you want to extend the power wires on your ESCs, maybe to mount them out on the arms under the motors. The general advice out there is to avoid this, extend motor wires if needed, but keep ESC power wires as short as possible. If absolutely necessary, extension of ESC power wires could require additional capacitors. Is this correct?
My thoughts follow. Comments and corrections are welcome.
The source of the problem is the very rapid switching that takes place in an ESC. Typically ESCs turn motors on/off anywhere from 8,000 to 16,000+ times per second. Within these brief on/off windows, the ESC adjusts the on time vs. the off time to control motor speed (see the linked review above for details). Skipping over the technical details behind the switching, it’s relatively accurate to say that an ESC’s pulsing demand for power results in voltage fluctuations on the input wires and the fluctuations are more severe the longer the length of power input wires to the ESC.
Wire length is an issue because the problem is driven by inductance on the power wires. The longer the run, the greater the inductance. The inductance resists changes to current flow and, in the presence of very rapid changes in ESC power demand, that ends up creating voltage fluctuations. By the nature of the problem, the peak voltage observed on the input lines at the ESC can be significantly higher than the battery source voltage. These voltage fluctuations can damage the ESC, with the primary point of initial failure being the capacitors themselves.
Conditional on an optimal build (more on this later), the broader layout of the multirotor (multiple ESCs, multiple power paths, etc.) does not change much about the nature of the problem. The fluctuations in voltage are most acute at the load — the ESC itself — and therefore any inherent capacitance that might be present in the build cannot directly address the issue. The only solutions are to limit the inductance and/or add capacitance at the ESC.
The best way to limit inductance on the ESC power connection is to limit the wire length, and, for any given length of connection, keep the wire pair tight (twisted or tight in parallel work about equally well). The worst outcome is a needlessly long power connection to the ESC with positive and ground wires separated.
Having limited inductance, one can add capacitors at the ESC. But whether this is really necessary is a complicated question. The answer, as best I can tell, is it depends.
There are many ways to examine this issue, and part of the problem is not directly observable. We can’t measure the extent to which the capacitor(s) on the ESC are internally fluctuating voltage. All we can observe is the voltage at the capacitor legs — i.e., the voltage at the ESC load point. As it turns out, this is does not appear to be a significant limitation.
To examine the question I have been testing the ESC I reviewed previously with various combinations of lead length to a battery and with various capacitors in place. The table below summarizes my results.
The values are voltage fluctuations as compared to the ESC’s stock capacitor setup (2 x 120μF Panasonics). The other capacitors in the table are what I had on hand and are all Rubycon ZLH series (a good choice for this application). For testing I removed the stock capacitors, so each item in the table reflects only the capacitors listed. The first line in the table reflects no capacitors at all (not recommended!). I tested with a battery, as opposed to a power supply, to best reflect real world experience. Voltage fluctuations were measured as AC peak-to-peak and AC RMS — both focused on deviations in voltage, ignoring the DC component. These measures presented highly correlated results, and the table is based on the more stable RMS measure.
First, note that the stock capacitors are not completely removing voltage fluctuations. We can improve things by adding capacitance, with improvement available all the way up to a huge 1200μF 63v capacitor (the largest I had).
Second, we can see that extending the power wires (either 4.5” or 9” — reasonable amounts for various arm lengths) results in higher voltage fluctuations, but we can mitigate those fluctuations by adding capacitors.
Third, compare the 6s results with no added length to the 4s results with 4.5” added length. The voltage fluctuations are nearly identical. Now one might say this is apples vs. oranges, and that would be correct. Yet, this is a major point of comparison and often ignored. True, adding length to power wires increases voltage fluctuations and puts more stress on the capacitors. But ESCs are made to operate under a variety of conditions. In particular, just about all ESCs operate over a significant voltage range and with tolerance of varying absolute deviations in voltage, including high frequency fluctuations, over that operating range. While the comparison is not perfect, there is some sense in saying that extending power wires at a given operating load is somewhat comparable to increasing the load itself if we focus solely on absolute voltage fluctuations at the ESC.
Finally, note how much extra capacitance it takes to offset added wire length. For a 4.5” length you need to roughly double the capacitance to offset the added voltage fluctuations. For an added 9” wire length the required increase in capacitance is roughly quadruple the stock amount.
So what to do? My view, based on these results, is that just working well within the rating of your ESCs is a viable approach. If you are running 4s power and want to extend the ESC wire length just get ESCs that can handle 6s. That’s not a perfect solution, but it’s defensible and arguably sufficient in reality.
The problem is most acute if you are extending line length for ESCs operating at their upper limit. In that situation, adding capacitors could be necessary. However, keep in mind that the relevant issue is total run from the battery to the ESC, and ESC makers know this. No decent ESC is going to fail based on a battery mount that is three or four inches longer on one build than on another. Keep the build sensible and mount your battery centrally and close to the power distribution point. Eliminate extra wire, long harness leads, etc. If you do that, extending the ESC power wires a few inches is probably not going to be a problem.
My thoughts follow. Comments and corrections are welcome.
The source of the problem is the very rapid switching that takes place in an ESC. Typically ESCs turn motors on/off anywhere from 8,000 to 16,000+ times per second. Within these brief on/off windows, the ESC adjusts the on time vs. the off time to control motor speed (see the linked review above for details). Skipping over the technical details behind the switching, it’s relatively accurate to say that an ESC’s pulsing demand for power results in voltage fluctuations on the input wires and the fluctuations are more severe the longer the length of power input wires to the ESC.
Wire length is an issue because the problem is driven by inductance on the power wires. The longer the run, the greater the inductance. The inductance resists changes to current flow and, in the presence of very rapid changes in ESC power demand, that ends up creating voltage fluctuations. By the nature of the problem, the peak voltage observed on the input lines at the ESC can be significantly higher than the battery source voltage. These voltage fluctuations can damage the ESC, with the primary point of initial failure being the capacitors themselves.
Conditional on an optimal build (more on this later), the broader layout of the multirotor (multiple ESCs, multiple power paths, etc.) does not change much about the nature of the problem. The fluctuations in voltage are most acute at the load — the ESC itself — and therefore any inherent capacitance that might be present in the build cannot directly address the issue. The only solutions are to limit the inductance and/or add capacitance at the ESC.
The best way to limit inductance on the ESC power connection is to limit the wire length, and, for any given length of connection, keep the wire pair tight (twisted or tight in parallel work about equally well). The worst outcome is a needlessly long power connection to the ESC with positive and ground wires separated.
Having limited inductance, one can add capacitors at the ESC. But whether this is really necessary is a complicated question. The answer, as best I can tell, is it depends.
There are many ways to examine this issue, and part of the problem is not directly observable. We can’t measure the extent to which the capacitor(s) on the ESC are internally fluctuating voltage. All we can observe is the voltage at the capacitor legs — i.e., the voltage at the ESC load point. As it turns out, this is does not appear to be a significant limitation.
To examine the question I have been testing the ESC I reviewed previously with various combinations of lead length to a battery and with various capacitors in place. The table below summarizes my results.
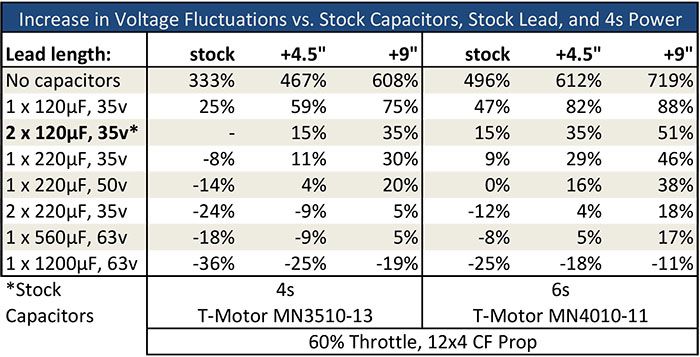
The values are voltage fluctuations as compared to the ESC’s stock capacitor setup (2 x 120μF Panasonics). The other capacitors in the table are what I had on hand and are all Rubycon ZLH series (a good choice for this application). For testing I removed the stock capacitors, so each item in the table reflects only the capacitors listed. The first line in the table reflects no capacitors at all (not recommended!). I tested with a battery, as opposed to a power supply, to best reflect real world experience. Voltage fluctuations were measured as AC peak-to-peak and AC RMS — both focused on deviations in voltage, ignoring the DC component. These measures presented highly correlated results, and the table is based on the more stable RMS measure.
First, note that the stock capacitors are not completely removing voltage fluctuations. We can improve things by adding capacitance, with improvement available all the way up to a huge 1200μF 63v capacitor (the largest I had).
Second, we can see that extending the power wires (either 4.5” or 9” — reasonable amounts for various arm lengths) results in higher voltage fluctuations, but we can mitigate those fluctuations by adding capacitors.
Third, compare the 6s results with no added length to the 4s results with 4.5” added length. The voltage fluctuations are nearly identical. Now one might say this is apples vs. oranges, and that would be correct. Yet, this is a major point of comparison and often ignored. True, adding length to power wires increases voltage fluctuations and puts more stress on the capacitors. But ESCs are made to operate under a variety of conditions. In particular, just about all ESCs operate over a significant voltage range and with tolerance of varying absolute deviations in voltage, including high frequency fluctuations, over that operating range. While the comparison is not perfect, there is some sense in saying that extending power wires at a given operating load is somewhat comparable to increasing the load itself if we focus solely on absolute voltage fluctuations at the ESC.
Finally, note how much extra capacitance it takes to offset added wire length. For a 4.5” length you need to roughly double the capacitance to offset the added voltage fluctuations. For an added 9” wire length the required increase in capacitance is roughly quadruple the stock amount.
So what to do? My view, based on these results, is that just working well within the rating of your ESCs is a viable approach. If you are running 4s power and want to extend the ESC wire length just get ESCs that can handle 6s. That’s not a perfect solution, but it’s defensible and arguably sufficient in reality.
The problem is most acute if you are extending line length for ESCs operating at their upper limit. In that situation, adding capacitors could be necessary. However, keep in mind that the relevant issue is total run from the battery to the ESC, and ESC makers know this. No decent ESC is going to fail based on a battery mount that is three or four inches longer on one build than on another. Keep the build sensible and mount your battery centrally and close to the power distribution point. Eliminate extra wire, long harness leads, etc. If you do that, extending the ESC power wires a few inches is probably not going to be a problem.